SST’S PATENTED AS-LED TECHNOLOGY IS THE MOST EFFICIENT INK CURING SOLUTION.
The revolutionary approach to LED curing is so efficient it delivers 24% more ink curing dosage while using 67% less energy than conventional LED. The longer exposure window and significantly less reflected energy are the keys. The result is exceptional performance with the lowest carbon footprint and the first solution to virtually eliminate heat from the printing process. Learn more about SST Led Technology and the resulting benefits for printers.
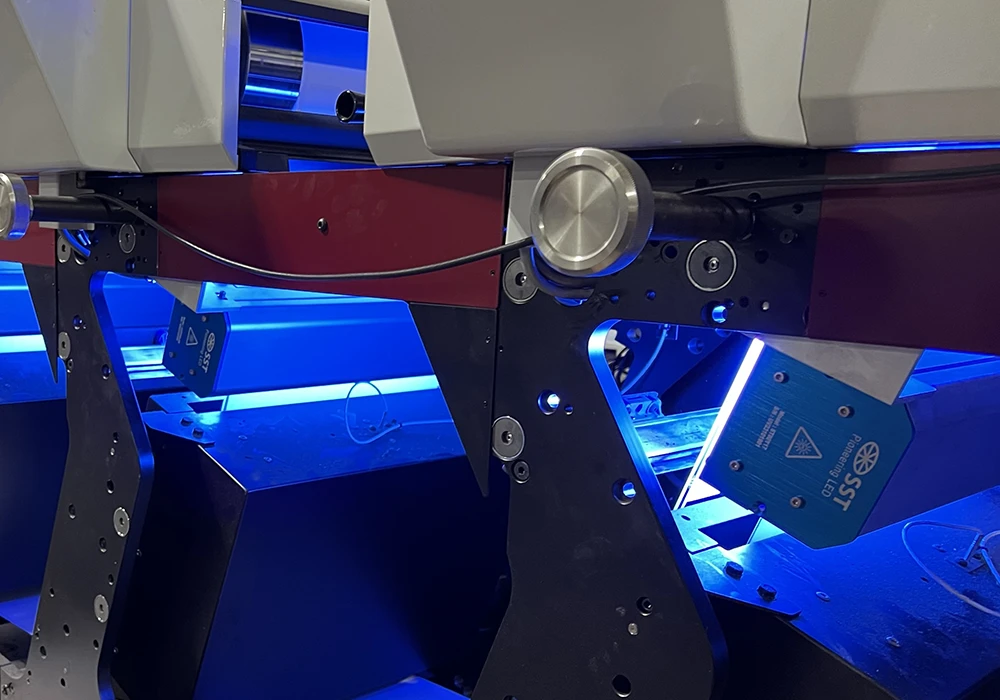
FLEXO PRINTING
UV or water-base presses are typically retrofit in about 8 hours. Mounting in addition to the existing system is usually possible to eliminate any risk of your LED transition. Chilling systems are no longer needed so you can now print shrink films even without chill drums. Learn more.
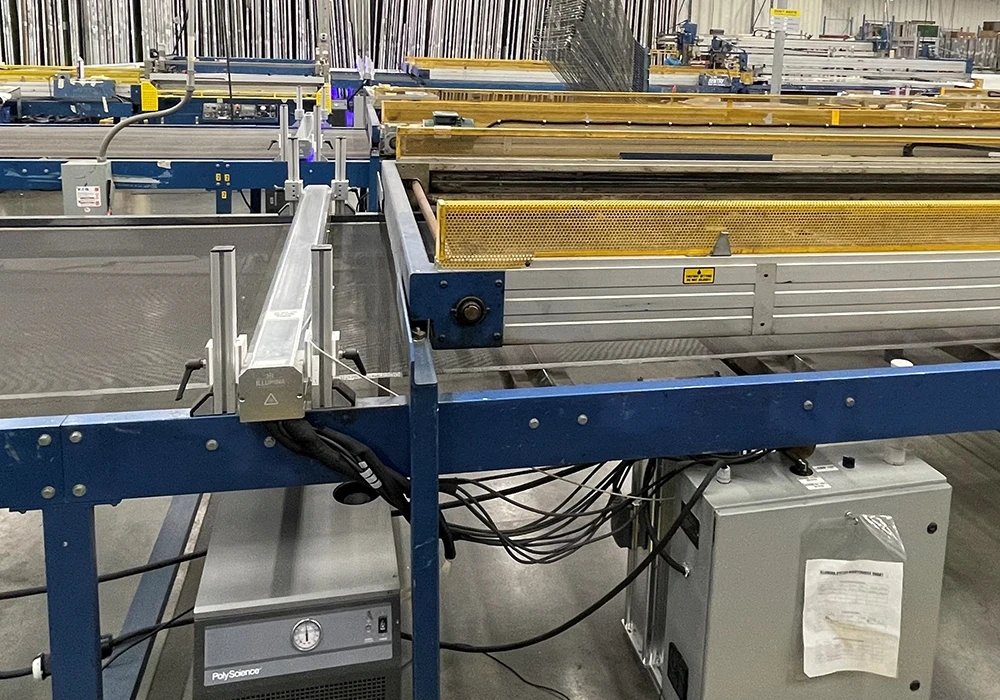
SCREEN PRINTING
Screen presses are typically retrofit (or mounted in addition to the existing system) in under 2 hours. Removing heat eliminates substrate shrinkage & fires, reduces “blocking” and HVAC loads, and provides a cooler working environment. Exhaust systems can also be disabled. Learn more.
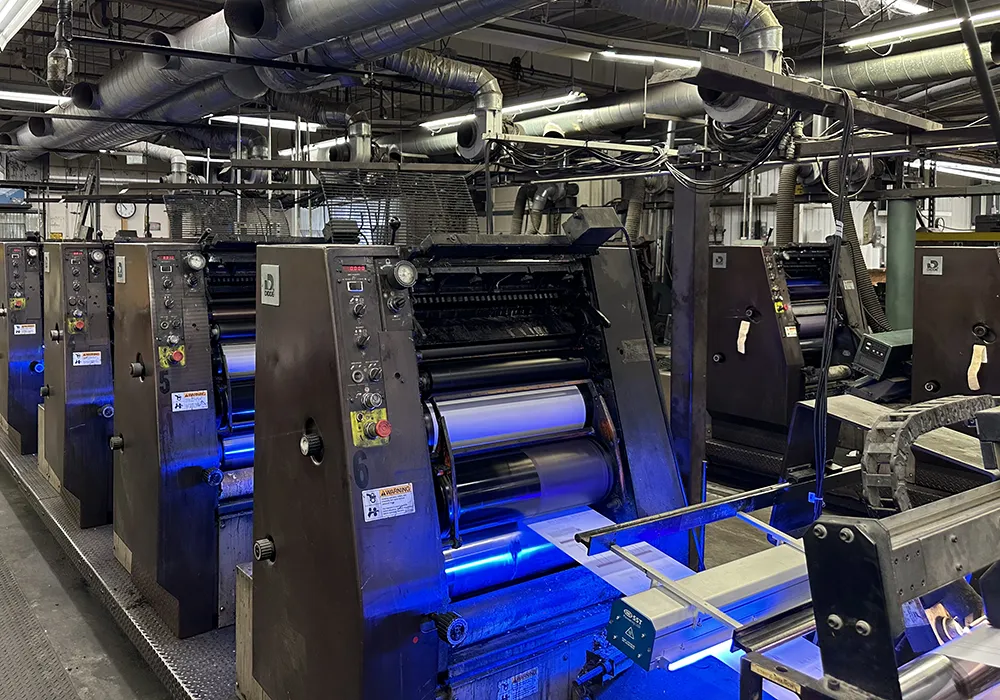
WEB-FED OFFSET PRINTING
UV Web or sheet-fed presses are typically retrofit in about 8 hours. Mounting in addition to the existing system is usually possible to eliminate any risk of your LED transition. Removing heat from UV provides a more comfortable working environment and significantly reduces AC load. Exhaust systems can also be disabled. Learn more.
ADDITIONAL SST LED APPLICATIONS + SERVICES
WHAT MAKES SST BETTER THAN CONVENTIONAL LED?
SUSTAINABILITY & SAVINGS UNIQUE TO SST LED
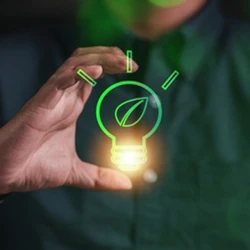
SST's patented design requires far less energy than UV, Conventional LED, or water-based drying systems. This not only provides the most environmentally friendly solution, but also the best ROI when making the investment in LED. Our unique approach to curing delivers the industry's lowest energy cost, best ROI and an average reduction of 100 tons of carbon emissions per press.
LEARN MORENEAR ELIMINATION OF HEAT FROM THE PRINTING PROCESS
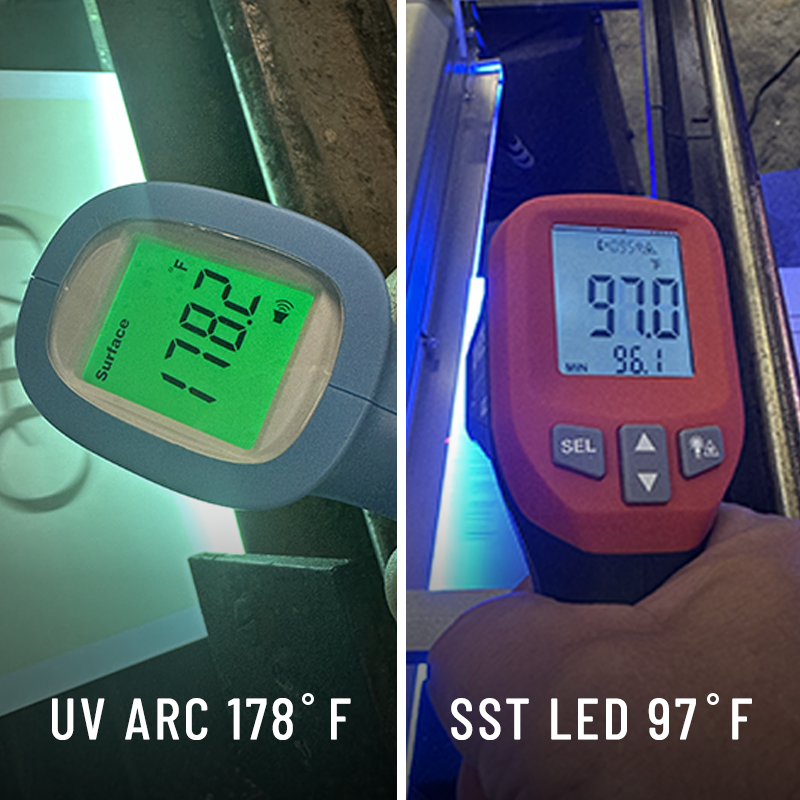
SST LED is the ONLY curing / drying technology that can make this claim. Our technology eliminates substrate and LED chip chilling systems as well as substrate shrinkage, breaks, and fires due to heat. Our system enables shrink film printing on presses with no chill system, faster print registration, and a reduced load on HVAC to recondition make-up air -- not to mention a more comfortable working environment.
LEARN MOREOUR LED TECHNOLOGY IS BETTER. READ OUR FEATURED CASE STUDIES TO LEARN WHY:

Label Source Reduces Energy Cost by $60,000+ Annually with 7 Screen Press Retrofit to SST LED
The COO/CFO shares the operational and financial benefits including 380,000 kWh and $60,000 + annual reduction in energy. Significant reduction in HVAC load with replacing very hot UV systems with SST LED and receiving a 31% rebate on the investment from their power supplier.